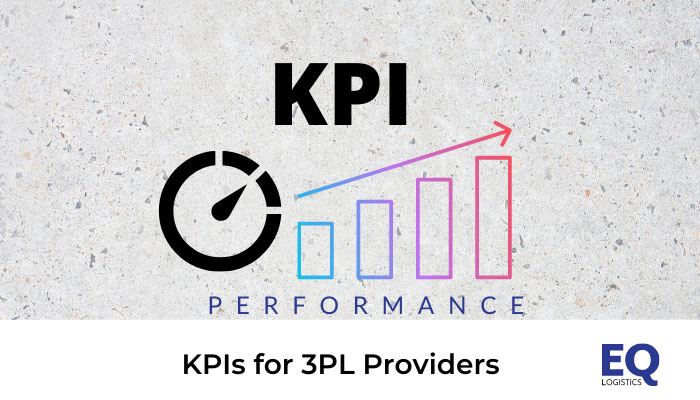
Effective supply chain and logistics managers rely on various measurements or Key Performance Indicators (KPI) to determine how their processes are performing and which areas need improvement. Let’s look at important KPIs for 3PL providers.
These critical measurements indicate how improvements can result in lower supply chain costs, maintain continuity of service, and result in higher levels of customer satisfaction.
Tracking Performance with Key Performance Indicators
To track and improve performance in a highly competitive environment, logistics management teams, whether in-house or third-party logistics providers (3PL), maintain sophisticated software systems that track each inventory unit from beginning to end.
Each phase of a supply chain, production, transportation, warehousing, and delivery can be measured for efficiency. While each overlap in certain areas, here is a closer look at KPI options useful for any 3PL warehousing function.
Measuring 3PL Warehouse Management Efficiency
Given the substantial amount of data available, a warehouse management group can establish a list of essential KPIs. Therefore these can help to foster significant improvements in service and profitability.
Key categories of KPIs for the warehouse function are inventory management and order fulfillment:
1. Management Key Measures
- Inventory Accuracy
Inventory accuracy is a calculation of actual inventory on hand versus the amount of stock on record. This number should be calculated on a per item or SKU basis. Applying these measures and striving for continuous improvement will improve the overall effectiveness of the inventory management systems. It can also indicate where problems may reside. Some issues may include pilferage, damage, errors in fulfillment, or other shortcomings.
- Turnover Rate
Turnover rate is the velocity at which the inventory of all or specific items passes through the warehouse. The impact of slow-moving inventory is tangibly felt in the carrying costs. If velocity or turnover rates improve, the total cost of the stock will decrease.
- Carrying Costs
Carrying costs represent the amount of money invested in purchasing, storing, and shipping an item. Finding ways to improve the turnover rate and lowering operating costs can improve the overall carrying costs of any items.
- Shrinkage
Shrinkage results from inventory loss due to theft, damage, misplacement, or unforeseen circumstances that can reduce the quantity of sellable items. A subset of Inventory Accuracy, improvement in shrinkage requires determining the source of the losses. This allows you to make improvements to minimize losses.
2. Order Fulfillment Key Measures
- Picking Accuracy
Picking inaccuracies can result in customer dissatisfaction and additional costs to replace the incorrectly selected inventory. More focused training and rewarding a culture of accuracy can eliminate this correctible problem. Calculate this KPI by dividing the total number of error-free orders by the total number of orders.
- Lead Time
Lead time, from the customer perspective, is the length of time from order placement to the time the order is delivered. Shortening this time frame can allow both the customer and the shipper to maintain lower safety stock levels and reduce inventory carrying costs. Reducing lead time is a significant marketing advantage as this allows the supply chain to operate more efficiently.
- Cost Per Unit
Cost per unit shipped is a calculation derived from the total costs involved in each and all deliveries. Calculations result from the unit carrying costs, including labor for picking, packing, and delivery plus fuel, equipment depreciation, utilities, and more. Improvement in each will yield a decrease in the overall cost per unit.
- On-Time Rate
Tracking how often deliveries are on-time is an essential measurement. Not only does this factor impact customer satisfaction, but it can also cause negative impacts on equipment utilization and even labor costs. Measure the On-Time Delivery Rate by dividing the number of on-time deliveries by the total deliveries in the period.
EQ Logistics Management
EQ Logistics, a 3PL provider with comprehensive warehousing and logistics service headquartered in Elkhart, Indiana, applies critical KPIs to all phases of its business. They are always striving to improve each client’s performance and profitability.
To learn more about EQ Logistics and their lineup of services or schedule a consultation, visit the EQ website at https://eqlogistics.us/.
Or, you may call EQ Logistics at (866)-847-8330.